Ray Gale, managing director of plastic packaging manufacturer Oaklair Ltd, acknowledged the escalating value of waste and set about investigating the most effective recycling solution for his Norfolk-based company. An investment in a Riverside waste baler soon proved worthwhile, with the machine having paid for itself within 12 months. Here he explains why the RWM 200 twin baler was the right choice… Background Norfolk-based Oaklair Ltd is a leading manufacturer of plastic packaging solutions, with clients including Wilco Motor Stores, Kettle Foods and Breckland Print to name just a few. Whether customers are looking for standard packaging or a custom-made offering, Oaklair believes in its ability to package anything, always with cost effectiveness, visual impact and practicality in mind. The Challenge Oaklair already had a system in place to recover plastic packaging waste and resell it in the form of a recycled material. Yet acknowledging the growing value of waste in the UK, Ray knew there was a more effective way to handle and transport this material. At the time it was simply being bagged and sent on in its current state, but the receiver sought a more compact bundle. The Solution A waste baling press allows users to take control of their dry recyclable materials by creating manageable bales. Further still, a multi chamber waste baler allow clients to handle more than one waste stream at once. In this scenario, the RWM 200 twin chamber baler posed the perfect solution for Oaklair. 90% of the company’s waste is either clear or black, and this machine enables the team to segregate and process both recycled materials at the same time. This saves on waste storage space and costs, and increases the efficiency of the waste handling process. Oaklair can bale two types of materials whilst utilising only one set of electric and hydraulic components. This achieves an output similar to that of two balers, but keeps maintenance and running costs to a minimum. The Results Oaklair was sending 110kg bags of recycled material to the receiver, but with the RWM 200 twin baler the team can send 300kg plastic bales. This saves on storage and transportation costs and increases the volume of recycled material they can sell in one go. As a result this vertical waste baler – the largest multi chamber baler in Riverside’s extensive range – has paid for itself in a 12 month period. But Ray is not just pleased with his machine because of this impressive return on investment. He elaborates: “This is an incredibly robust piece of equipment that has been engineered to satisfy all of our requirements. It was supplied with first class training, with members of our team receiving competency certificates once their proficiency had been assessed by Riverside. It is easy to use and extremely reliable. We have experienced no problems since the machine was installed a year ago.”
Riverside waste baler pays for itself in 12 months
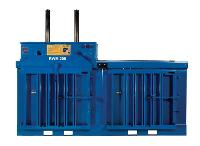