Background Links to Work is a “work preparation and supported employment service” backed by Walsall Council. Providing manufacturing, assembly and packaging services to businesses in the region and beyond, Links to Work acts as a training centre delivering employment and re-enablement skills for people with physical and mental disabilities. At the same time this social initiative enhances employees’ levels of confidence, independence and inclusion in society. The Challenge With customer contracts totalling approximately £200,000 last year, Links to Work is successfully providing a number of valuable opportunities for individuals looking to access or re-enter the world of employment. But as the level of work has grown – especially for clients seeking repackaging services – so too has the amount of cardboard and polythene waste being handled by this West Midlands organisation on a weekly basis. Committed to upholding environmentally-friendly working practices, Links to Work therefore founded a small recycling operation which has not only enabled such waste to be recovered and reused; it has also meant a revenue can be obtained from the sale of this material. But with ever-increasing volumes of cardboard and polythene being handled, the organisation’s existing compact waste baler could no longer provide an adequate waste management solution. A machine upgrade seemed like the obvious next step, but Links to Work had to be certain that an investment in a new, larger machine could be justified. The Solution Extensive industry research led Links to Work Joint Site Manager, Richard Butler to Yorkshire-based Riverside Waste Machinery. Conversations with Riverside’s managing director and experienced waste baling specialist Jonathan Oldfield followed, with an RWM 400 mill size waste baler appearing the best fit solution. Riverside did not have a place on the council’s preferred supplier list. However believing they were the right machinery provider for the job, Richard therefore drove his own business case for an RWM baler investment. He explains: “Whilst price was an influential factor when deciding upon our waste baler of choice, it was also a case of assessing the overall value of the machine not just the initial capital outlay. Moving forward, machinery reliability, ease of maintenance and competitively priced consumables mean that the long term cost of the baler is much more attractive than competitors’ offerings. “I also learned from Jonathan that this mill size waste baler would solve our current waste handling issues, quickly achieve a return on investment and provide technology longevity as our recycling operation continues to evolve.” The Results With a press force of 25 tonnes and capable of producing bales of up to 450kg, this machine now gives Links to Work the capacity to handle much greater volumes of packaging waste. As Richard elaborates, there are other benefits too: “The RWM 400 is incredibly easy to operate, and the speed with which it eats up our dry recyclables is exactly what we were looking for. It has already started to pay for itself in only a matter of weeks. “We are somewhat future-proofed as well, in terms of the volume of waste and material types we can handle. For instance if we pick up more heat-shrinking or blister packing jobs, then our baler will continue to support us as our initiative grows.” Links to Work has established contracts to collect waste from other companies in the local area too. Not only will this increase the revenue that the initiative is able to recoup when selling recyclable materials onto local processing plants, but it also alleviates the waste handling headache being experienced by these external organisations. It is hoped that this service provision will expand moving forward, thus heightening Links to Works’ recycling operation and providing a greater number of employment opportunities for local people with disabilities.
Riverside waste baler enhances recycling capabilities of social initiative
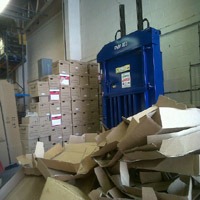