Waste baler servicing – prevention is cheaper than cure
It is an overused phrase, and a bit of a cliché, but the age-old saying ‘prevention is cheaper than cure’ really is true. Just as we send our cars to be routinely inspected by mechanical experts to ensure they are in correct working order, we should adopt the same proactive approach to looking after waste balers too. So how can we help?
Three affordable service and maintenance packages to choose from:
*We will not provide cover for operator misuse
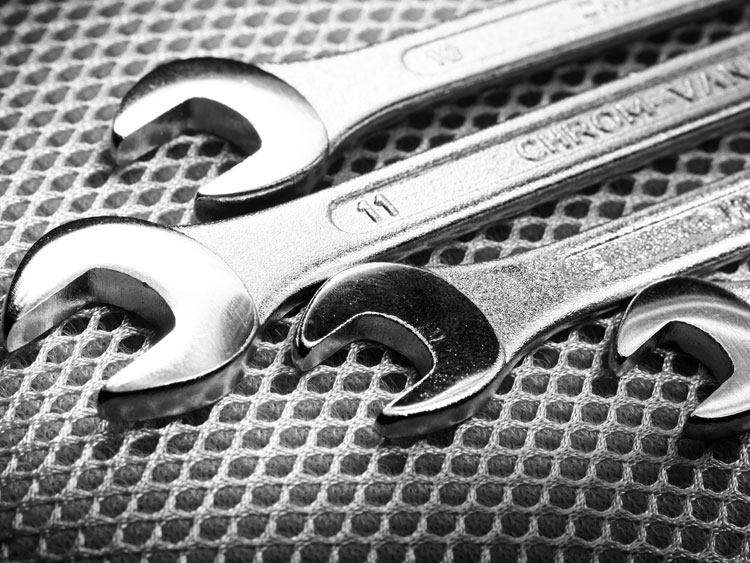
Regular servicing
As standard, we recommend a bi-annual service so that the same engineering experts who have installed your waste baler, can come and give it a thorough inspection twice a year before the unexpected happens! That said, talk to us about your baler usage, as we may advise a different servicing frequency better suited to your operations.
Very much a machinery health check, a baler service strives to optimise the ongoing performance of your equipment. We look for evidence of wear and tear, and dig deep to uncover any indications of potential future problems. We call this approach ‘preventative maintenance’. This reduces the likelihood of any unplanned downtime and minimises the future expenditure required to undertake potentially costly repairs. This servicing expertise is available throughout the UK, and on any waste baler regardless of the manufacturer.
Operator training
By design, our waste balers have been engineered so that they’re easy to use. That simplicity also extends to the maintenance – in fact, as part of the operator training we deliver at the commissioning stage, we advise a number of quick steps that clients can undertake to keep their equipment running smoothly.
Did you know we offer refresher training too, to ensure operators maintain their knowledge and certified competence?
Baler repairs
If you don’t have a waste baler servicing contract, we can still help with any repair requirements that you have. Our specialist engineers will aim to resolve the problem as quickly and cost-effectively as possible, before leaving you with advice to help prevent any recurring faults or future technical problems.
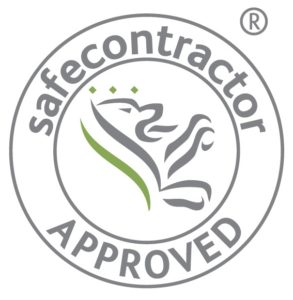