Background Retail supply chain specialist Dee Set Complete Retail Solutions wanted to take its recycling strategy up to the next level at its 178,000 sq ft warehouse in Stoke-on-Trent. Always striving to ensure its operations are managed as efficiently as possible, the £120m turnover company decided it was time to upgrade its waste baling technology. Providing logistics and fulfilment services to major retailers such as Asda, Morrisions and Sainsburys, Dee Set was not only looking for waste management equipment that could cope with the very high volumes of waste card it produced but that would pay for itself within 12 months. The Challenge Dee Set had been using a rented compactor and baler to process its warehouse waste. However, a review of hire and lease agreements led Health & Safety Manager Andy Walker to consider purchasing the new equipment he had in mind. Armed with the benefit of previous experience, Andy knew he wanted a mill size baler and it didn’t take him long to select Riverside as the supplier. “I had used mill size balers before at another company so I know just how effective they are not only in terms of improving the throughput of waste but in reducing transport costs. “I contacted a number of suitable suppliers and whilst assessing the quotes I received I was particularly impressed with Riverside’s approach – good pricing, no hard sell, great service – it was a winning combination!” The Solution Following Riverside’s advice, Andy decided the best-fit machine for his recycling requirements was a RWM 500 mill size baler. The RWM 500 has a 50t press force and produces 1200 x 1500 x 760mm bales in just 40 seconds. This particular baler is very popular with businesses that use shipping containers and flat-bed trailers to transport their waste. The larger bales maximise load capacities and therefore significantly reduce costs. The Results Dee Set is currently baling approximately 300t of cardboard waste per year which equates to 40 bales per month. Its existing baler is used to process plastic shrink wrap waste and the new machine is dedicated to dealing with the vast amounts of cardboard packaging waste generated by its warehouse operations. The company is now able to manage its waste streams far more effectively; card has a designated baler and is no longer mixed with other waste materials. This in turn has reduced the number of compactor collections required and has contributed to significant cost benefits. In fact the cumulative savings – fewer compacted waste loads, reduced waste processing costs and waste rebates – have ensured that the RWM 500 has paid for itself in just 6 months. “The benefits of the new baler really are far reaching,” adds Andy. “It has improved our internal working procedures, it’s helping cut transportation costs as well as reducing the amount of waste going to landfill and it is making us money. “There are the obvious cost and environmental savings of course but for us another major benefit is being able to prove to our customers that we are an environmentally responsible supplier. We are very proud to work for some of the most successful names in retail and we aim to exceed their expectations with all aspects of our business.” Visit Dee Sets website www.deeset.co.uk
Riverside waste baler is best-fit for global business
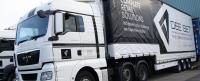