The background Established in 1991, Yorkshire-headquartered packaging company Greyhound Box Ltd is well known for providing a highly reliable and comprehensive packaging program – including design, manufacturing, and waste management consultancy. As a British manufacturing company, Greyhound seeks to work directly with its customers to optimise supply chains and reduce carbon footprint – while boosting the bottom line of a business. The challenge The Greyhound Box team has spent the last five years improving its on-site materials handling efficiencies, as the firm prepares for 5% growth over the next 12 months. And, despite the devastating effects of COVID-19 across the globe, increased demand for packaging – to house much-needed supplies such as hand sanitiser and PPE – ensured that business at the Leeds-based factory ramped up. Louise O’Brien, managing director at Greyhound, said: “We’d outgrown our old baler, and it no longer fitted our needs – it became clear that we were using excessive staff hours to operate and maintain it. So, in line with our outlook on saving time and money as an organisation, we began to explore alternatives.” The team therefore sought out a faster solution to handle excess cardboard, and contacted Jonathan Oldfield at Harrogate-based Riverside Waste Machinery, due to an existing relationship with the firm. The solution Following consultation with Jonathan, the RWM compactor – with 1100 litre bin lifter and eight wheelie bins to enable ease of movement of the cardboard – was recommended and then installed, as a crucial next step in the company’s plans for the future. Discussing the investment, Jonathan commented: “When we installed the RWM 400 waste baler back in 2005, Greyhound Box created far less waste. However, in-house production levels have continued to rise – and as a result, the compactor was an obvious choice.” Safely installed during UK lockdown, this latest addition to Greyhound’s machinery range has further solidified the more efficient waste-handling process – not least due to the machine’s impressive speed of operation. The results Typically larger than a vertical baler, compactors have a greater waste-handling capacity, with the newly installed model able to easily process the 345kg of cardboard produced by Greyhound daily, in a fraction of the time. Louise said: “A member of staff would spend three hours a day baling cardboard in the factory – sometimes even a full day if there was a backlog of material. This would greatly affect production as staff were lost to the process. “Now, with the compactor in place, we use up less than two and a half hours a week loading the machine – it has made a real difference in terms of time savings!”
Cardboard box manufacturer invests in Riverside compactor
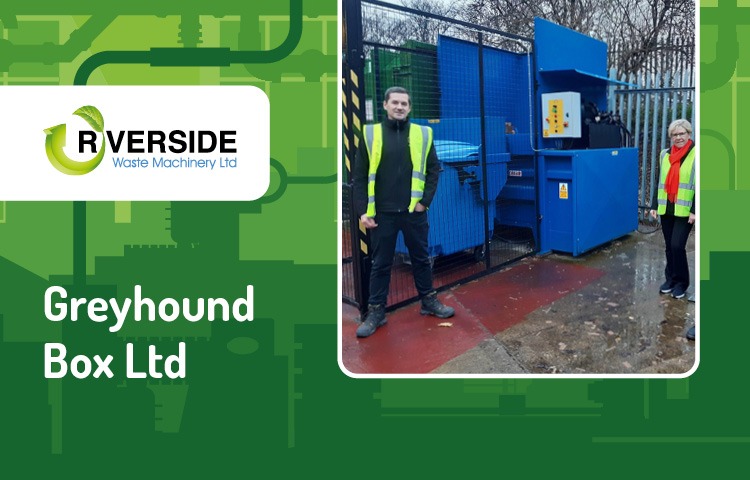